Nacionalização no Prosub – fabricação do casco resistente
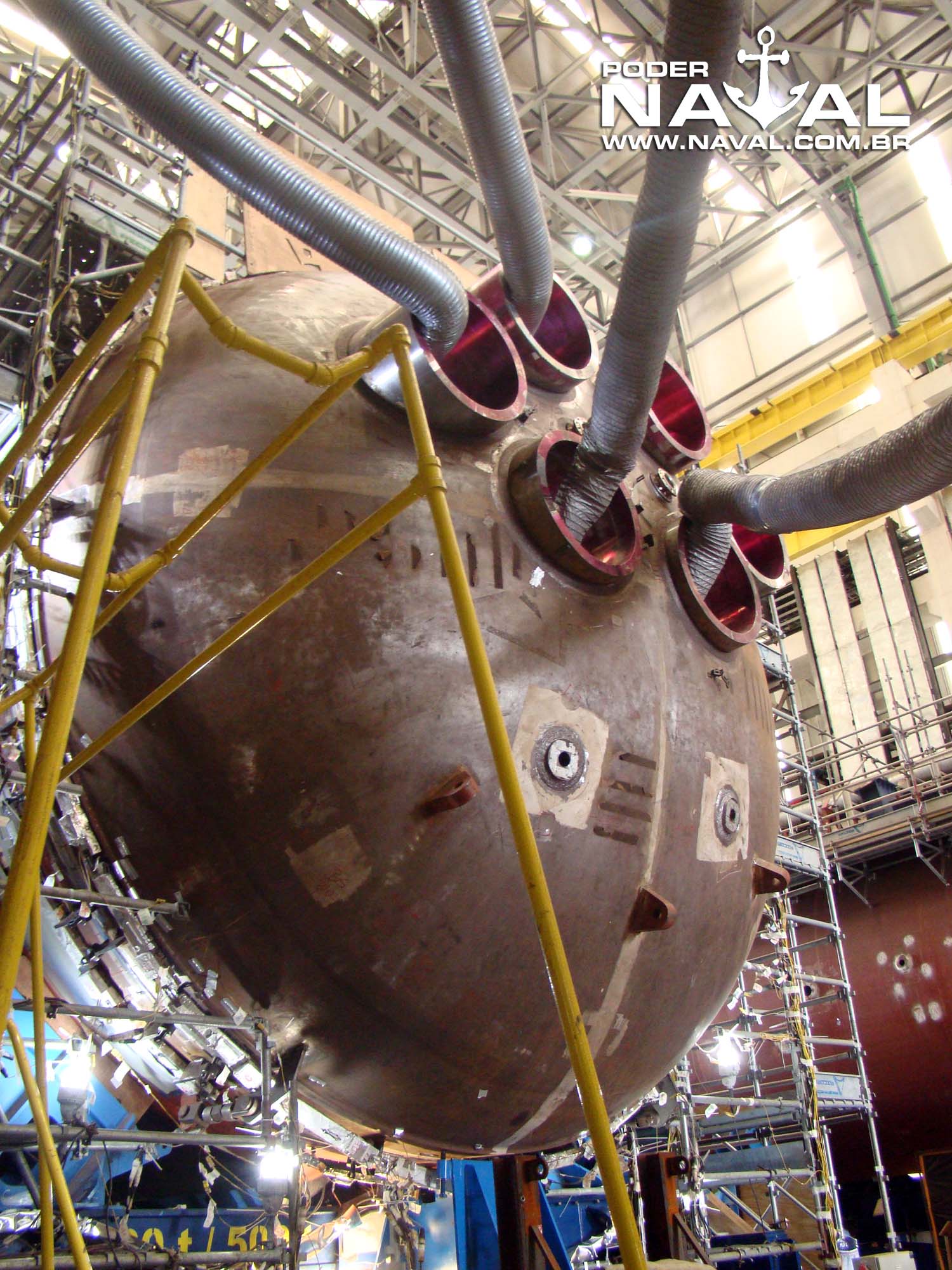
Por Guilherme Poggio
A década de 1980 foi importante para a Força de Submarinos, pois ela marcou o início da fase em que o Brasil deu partida na busca de sua autossuficiência para projetar e construir a sofisticada arma de guerra naval que é o submarino.
Naquela década, o contrato assinado com o estaleiro alemão HDW iniciou a capacitação técnica brasileira para a construção do primeiro submarino no Brasil. Fruto desse contrato, que estabelecia a construção de um submarino IKL 209 na Alemanha e os demais no Brasil, engenheiros e técnicos de diversos setores realizaram estágios no estaleiro alemão. A Nuclep, empresa brasileira que fabrica estruturas pesadas, qualificou-se para produzir a maior parte das seções do casco resistente dos submarinos (ou casco de pressão, pois é o que resiste à diferença entre a pressão do mar externa e a pressão atmosférica interna).
Porém, algumas importantes partes foram importadas diretamente da Alemanha. Dentre estas estavam as chamadas “calotas”. Calotas são peças metálicas com superfícies curvas que compõem as extremidades do casco resistente.
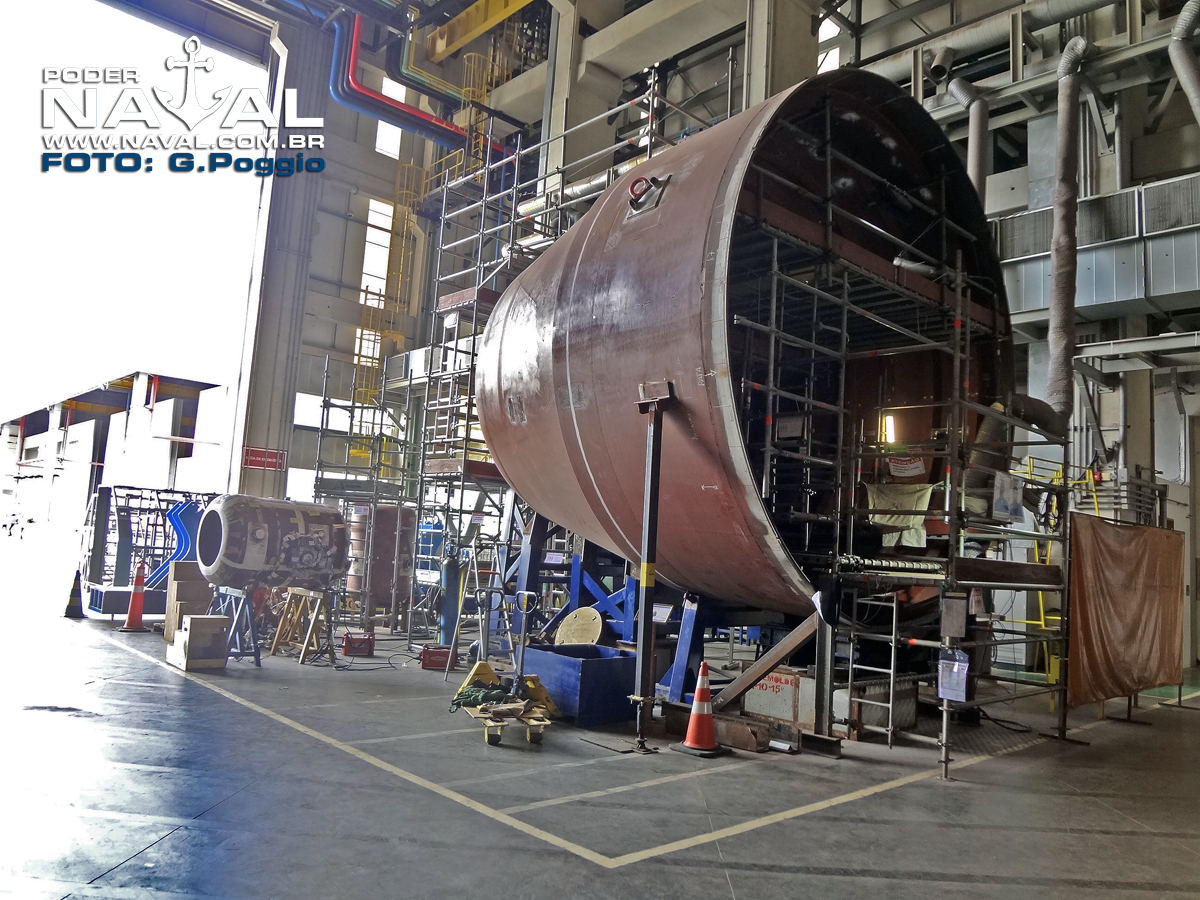
Ao contrário das seções que foram produzidas pela Nuclep para os submarinos IKL 209 da Marinha, as calotas necessitam de maquinário específico e qualificação de mão de obra diferenciada. Obviamente que tudo isso implica em aumento de custos.
Como o contrato de construção dos submarinos com a Alemanha foi assinado numa época de grave crise econômica, o programa sofreu limitações orçamentárias e muitas etapas da construção do casco resistente não puderam ser nacionalizadas. As calotas eram algumas dessas estruturas que não foram nacionalizadas.
Com o Prosub (Programa de Construção de Submarinos) a Marinha quis dar um passo à frente. Além de produzir novamente as seções circulares no Brasil (refazendo a antiga parceria com a Nuclep), ela buscou a nacionalização da produção das calotas e outras estruturas do navio. Ou seja, desta vez o domínio completo do processo fabril do casco tornou-se a meta da instituição.
Prensa hidráulica
Para a produção das calotas a Marinha teve que adquirir um equipamento especialmente desenvolvido para este fim. Trata-se de uma prensa hidráulica de grandes dimensões. O projeto da prensa e a sua fabricação ficou por conta da empresa Prensas Schuler, subsidiária da Schuler alemã e localizada na cidade de Diadema (SP). É importante destacar que o projeto da prensa contou com o know-how brasileiro desta empresa que possui mais de 50 anos de Brasil.
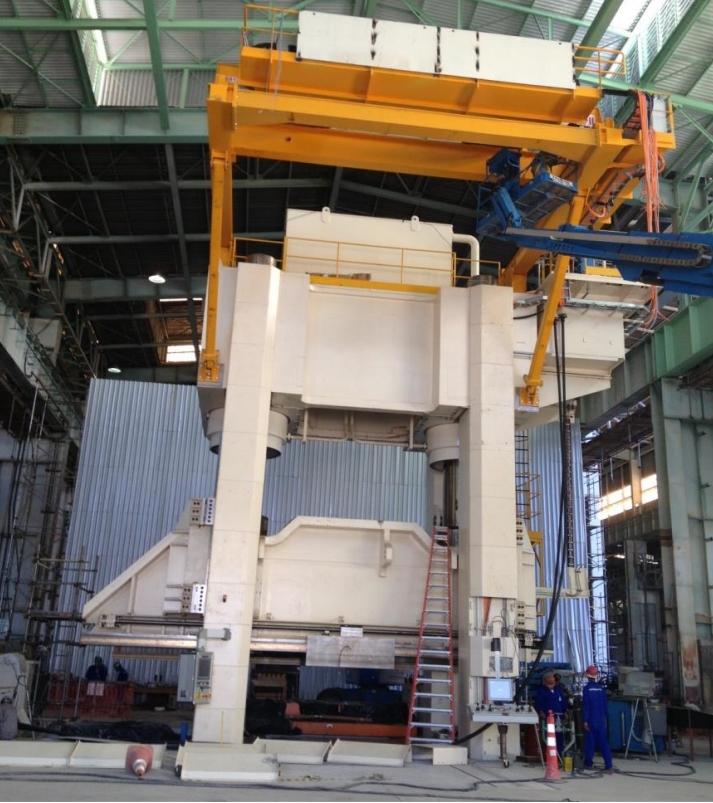
A prensa hidráulica com capacidade para 80.000 Kn de força de prensagem foi desenvolvida especialmente para o dobramento de chapas de aço especiais com 100 mm de espessura ou mais. Ela possui dois cilindros de 40.000 Kn acionados por um sistema hidráulico e elétrico especial e circuitos servo-comandados. O reservatório de fluido hidráulico armazena 14.000 litros e está localizado no cabeçote dela.
Não bastava apenas adquirir os equipamentos corretos. Era preciso dominar a técnica para dobrar as chapas. Para esta etapa técnicos e engenheiros brasileiros da empresa Itaguaí Construções Navais (ICN), uma Sociedade de Propósito Específico (SPE) criada pela CNO e pela DCNS (atualmente Naval Group) para construir os quatro submarinos convencionais e o nuclear do PROSUB, foram enviados à França. Nas instalações de Cherbourg, onde o Naval Group constrói seus submarinosos profissionais brasileiros foram treinados no processo “on-the-job-training” (OJT), acompanhando a fabricação das calotas do SBR 1.
Por questões físicas, logísticas e organizacionais a prensa hidráulica foi instalada no terreno da Nuclep, embora seja propriedade da Marinha. A Nuclep não detém a tecnologia de fabricação de calotas. Apenas o pessoal da ICN possui esta qualificação. Desta maneira, toda a fabricação do casco resistente ficou concentrada na Nuclep, cabendo à UFEM (Unidade de Fabricação de Estruturas Metálicas) apenas a fabricação das chamadas “estruturas leves”, além de de outras atividades fundamentais (em breve publicaremos matéria exclusiva sobre a UFEM e mais detalhes sobre os trabalhos ali desenvolvidos).
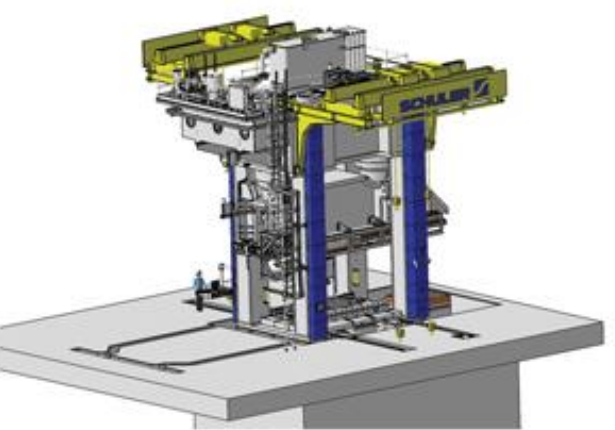
As duas principais peças produzidas pela prensa hidráulica de 80.000 Kn são as calotas de vante e de ré. Em linguagem simples elas representam a tampa de proa e de popa do cilindro que é o casco de pressão do submarino. Mas estas não são as únicas calotas que existem num submarino.
Todo casco de pressão possui apêndices, que são estruturas colocadas nas aberturas deste casco. Os apêndices incluem mastro penetrante (periscópio de ataque), tubos lança-torpedos (TLP), escotilha de resgate e outros. Em alguns destes apêndices existe a necessidade da fabricação de calotas. Este é o caso da escotilha de escape de emergência, que pudemos fotografar na UFEM (ver foto abaixo). A peça possui calotas nas duas extremidades onde futuramente serão instaladas escotilhas para operações de resgate ou embarque e desembarque de mergulhadores de combate (MEC) com o submarino submerso.
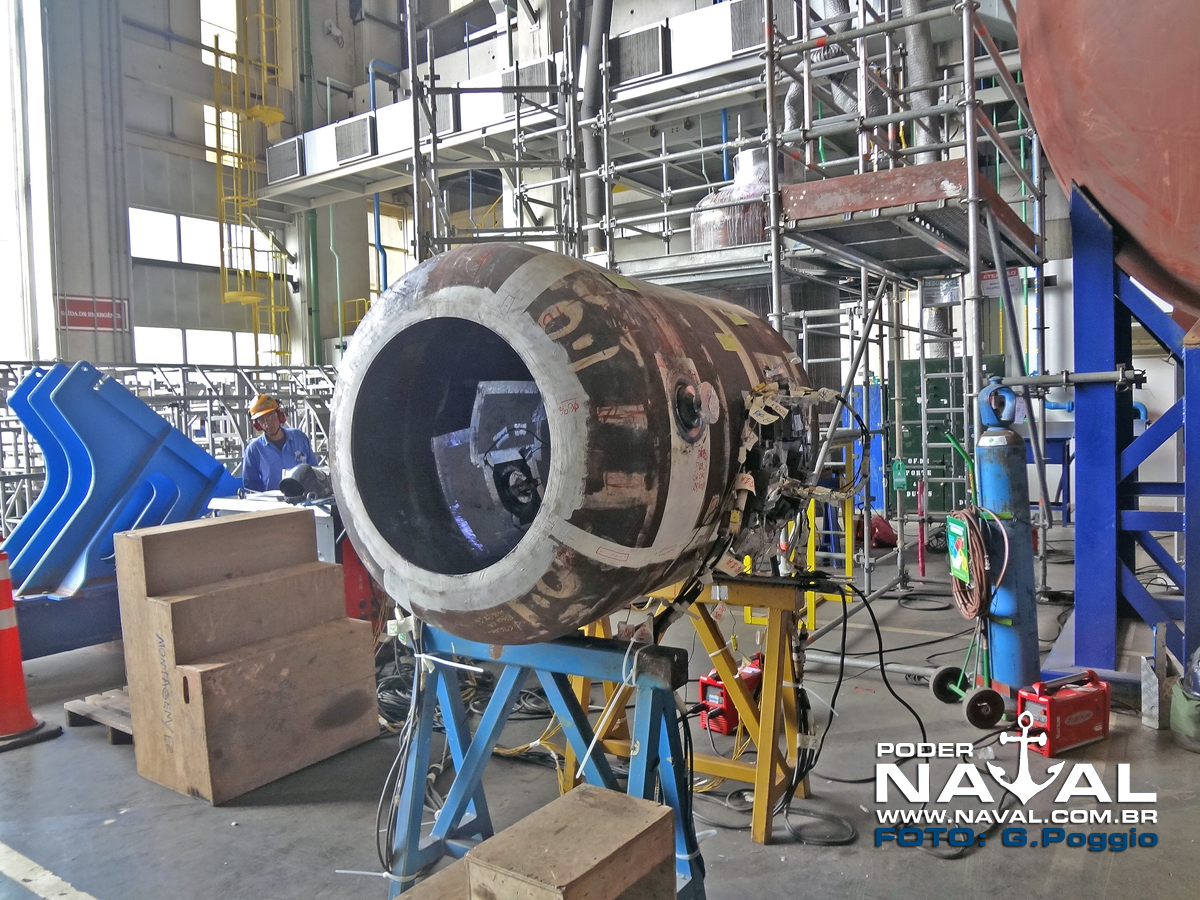
TLP
Outro item que mereceu atenção da Marinha foi a nacionalização dos TLP (tubos lança-torpedos). Cada SBR possuirá seis TLP que, como mencionado acima, comporão parte dos apêndices do casco de pressão.
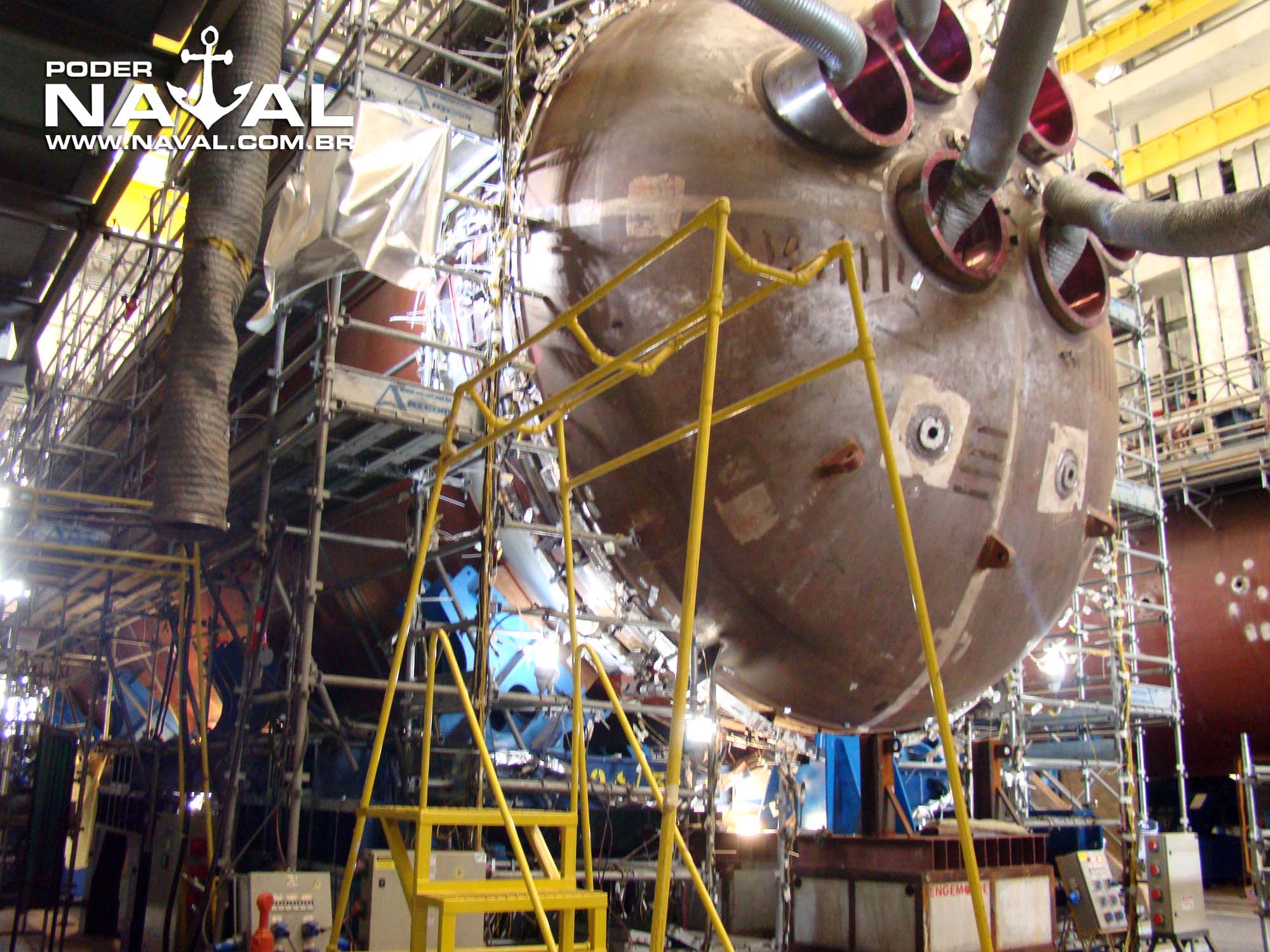
Para receber a tecnologia de construção dos TLP a Marinha selecionou a Bardella S.A. Indústrias Mecânicas. A Bardella é uma empresa nacional que atua no setor de bens de capital (máquinas e equipamentos) e mais de cem anos de existência, tendo contribuído com o crescimento e desenvolvimento do país durante todo esse tempo.
Mas a grave crise econômica que atingiu o Brasil a partir de 2015 afetou a empresa diretamente. A queda na produção e os problemas financeiros começaram naquele ano e se agravaram em 2016. Em 2017 a receita líquida da empresa foi 48% inferior à receita do ano anterior. Diante da situação financeira precária da empresa ela não poderá atender a Marinha.
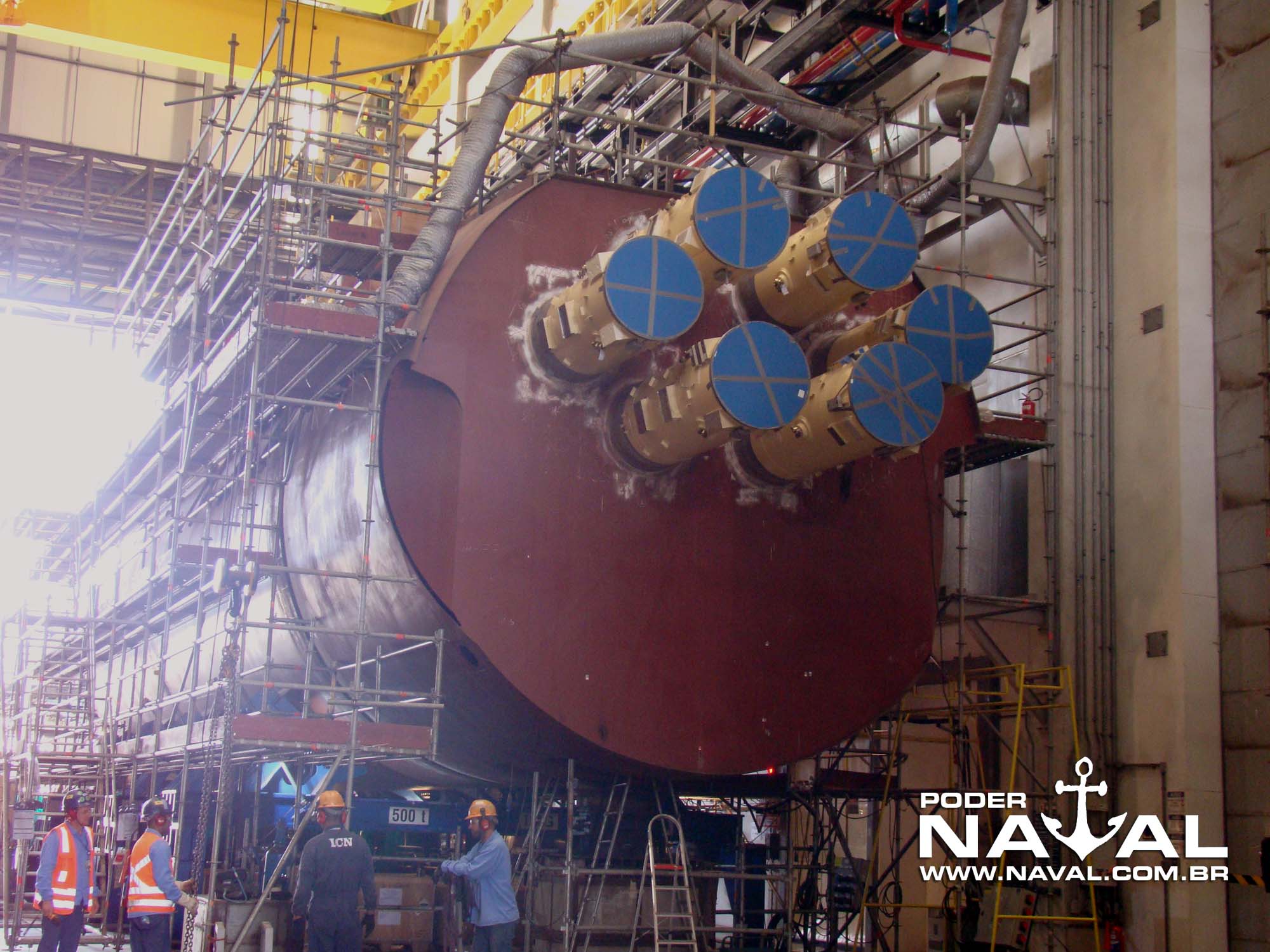
Para que o processo de construção dos SBR não sofresse novos atrasos a gerência do programa tomou a decisão de importar os TLP diretamente da França para todos os quatro submarinos convencionais (e não só para o SBR como era inicialmente previsto). Em relação ao SNBR esta questão está em aberto (construir aqui ou importar).
Mas a Bardella não estava envolvida apenas no processo de construção dos TLP. Ela também estava encarregada de receber tecnologia para nacionalizar o sistema de movimentação de armas, cuja intenção era de produzir o sistema para os SBR 3 e 4.
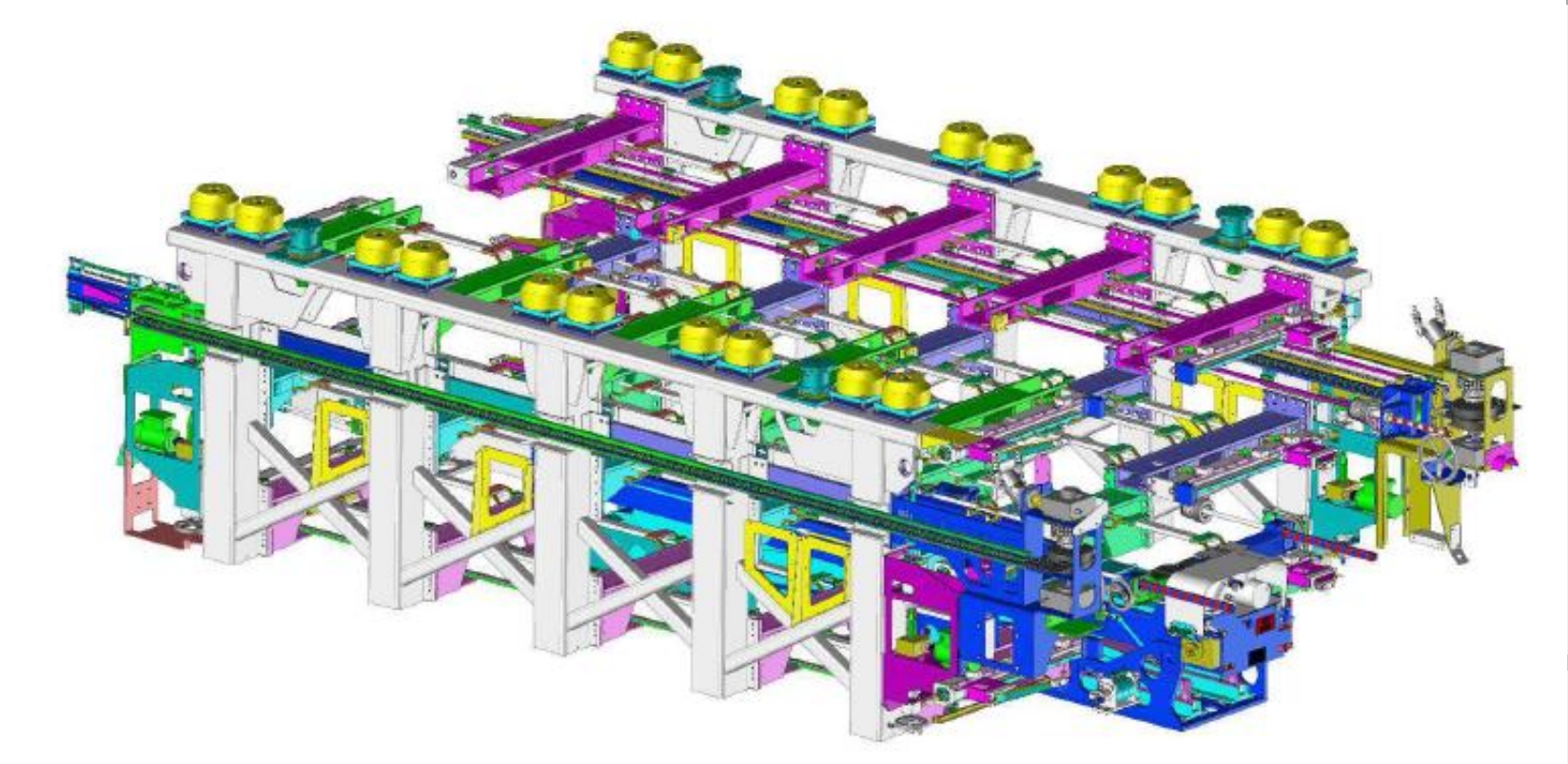
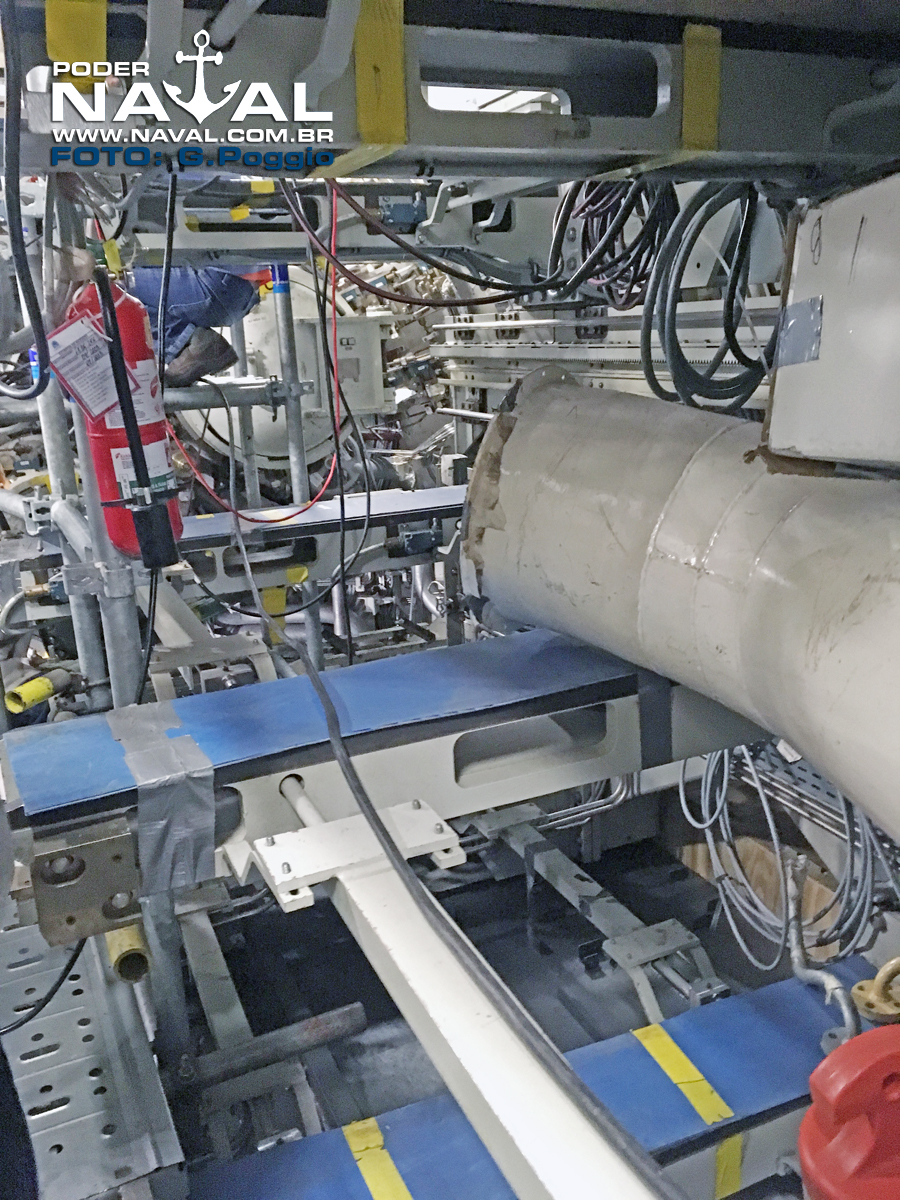
O caso da Bardella exemplifica apenas uma das várias dificuldades do processo de nacionalização. Como muitas das encomendas das Forças Armadas são de pequeno volume, a maioria dessas empresas privadas necessita de um mercado civil interno ou de exportação para sobreviverem.
O problema é a falta de um ambiente de negócios favorável no país, onde os ciclos econômicos não sejam tão agudos e não afetem profundamente as empresas. A FAB conheceu bem esse problema na época de nacionalização de componentes para o programa AMX. Alguns dos fornecedores nacionais que receberam transferência de tecnologia simplesmente não conseguiram sobreviver diante das sucessivas crises econômicas e afetaram o suprimento de componentes para a frota.
Prosub proporciona um avanço ímpar na indústria pesada do país.
A MB trava enormes batalhas nos bastidores para conseguir por em pé este programa.
Seria muito bom se o PN pudesse nos passar alguns destes causos de bastidores.
Eu queria ver como está o estaleiro em si atualmente
Uma vista geral de como anda a obra….
se puderem postar algo, seria muito bom!
Abraço
Trataremos desse assunto em futuro post, Rafa_positron
Obrigado
🙂
Rafa, não sei se percebeu, mas estamos publicando uma série de matérias desde a semana passada. Já mostramos obras no prédio dos simuladores e no de manutenção de sistemas. Dê uma olhada nas anteriores e, se não encontrar o que procura, basta aguardar pelas próximas, pois ainda há muito conteúdo e fotos para publicar.
Opa!
Vem mais por ai?
Coisa boa!
Fico ansiosamente no aguardo!
Como já comentei em outro post, desenvolver e/ou aplicar tecnologia em projetos no Brasil não é para os fracos.
Parabéns mais uma vez a MB.
Mas aí fica a dúvida, será que só a Bardella teria condições de receber essa transferência de tecnologias?
Aqui em Minas temos a Orteng e diversas empresas com capacidade para tal função.
Isso para não falar na empresa que fabrica os SLT,s para navios de superfície.
Acho que faltou uma pesquisa mais ampla de mercado, em minha modesta opinião.
Uma solução seria disseminar o conhecimento para um conglomerado de empresas nacionais, gerando assim demanda para diversas empresas.
Cada empresa do conglomerado ficaria responsável por uma parte do sistema, cabendo a MB o domínio do sistema completo.
A seleção de empresas que fazem parte da cadeia de fornecedores de um projeto dessa magnitude, passa por RFP, análise técnica, preço, etc.
Sem dúvida, a empresa escolhida venceu outras concorrentes num certame auditado. Fique tranquilo, a MB está fazendo um brilhante trabalho nesses submarinos.
Não só isso. A MB fez diversas palestras pelo país convocando empresas a participarem do programa. Ninguém que entrou, entrou com a faca no pescoço. Quem está no program é porque quis participar e se submeteu às exigências do contratante.
Bacana, mas não tem VLS. Um retrocesso…
Não precisa de VLS.
VLS ? , Oi ?!
Os SSNs classe “Astute” que ainda encontram-se em em produção também não são equipados com VLS assim como a nova geração de SSNs franceses não será …então não trata-se de “retrocesso” e sim da necessidade de cada usuário.
Não necessita-se de lançadores verticais para lançar mísseis.
VLS para navio de superfície significa que o reparo não precisa conteirar. Em submarino isso não tem o menor cabimento.
Ter VLS significa abrir mais uma janela no casco de pressão, reduzindo a resistência e aumentando mais um ponto de fraqueza na estrutura.
Atualmente os TLP fazem o trabalho de um VLS. Por ali você pode lançar torpedos, mísseis, minas, etc.
os misseis de cruzeiro já são lançados pelos tubos dos torpedos. Aprendi isso aqui no PN.
Ultimamente esses tratados internacionais antimísseis só tem servido para os grandes limparem o traseiro com eles. Quem sabe o Brasil possa no futuro ter pelo menos um MRBM, nuclear ou não.
“Ultimamente esses tratados internacionais antimísseis só tem servido para os grandes limparem o traseiro com eles.”
Não é bem assim.
Acho que você está mal informado ou ideologicamente influenciado.
O acordo com o Irã manda lembranças.
Qual é o problema com o acordo com o Irã ?
Quebrado por um de seus signatários sem motivo plausível.
@Defensor da Liberdade
Sim, e como diz a música:
“Sempre foi assim. Assim será….”
Cara, pesquise antes de sair fazendo afirmações categóricas pela internet. A MB não colocou lançadores verticais nos SBR porque não quer. Não existe tratado a proibindo.
Inclusive o gerente do projeto já respondeu em entrevista a outro site que o SNBR-1 tambem não terá VLS, porque não faz sentido complicar o projeto de algo que está sendo feito pela primeira vez, mas que deixarão a possibilidade em aberto para os próximos submsrinos nucleares.
A NUCLEP não poderia absorver a tecnologia de desenvolvimento e fabricação do TLP? a UFEM não teria condições de fabricar o sistema de movimentação de armas?
Pergunto não só pela capacidade técnica do pessoal da NUCLEP e da UFEM, mas pela disponibilidade para mais essas empreitadas.
Abraços.
Alisson Mariano, a ideia era decentralizar e não concentrar tudo. A Nuclep e a UFEM já estão bem sobrecarregadas. O trabalho é intenso nas duas e tudo precisa ser feito ao mesmo tempo. Até mesmo na França os TLP não são feitos no estaleiro de Cherbourg.
Talvez não seja tão difícil encontrar fornecedor(es) nacional(ais) para os dois sistemas, pelo menos, para o SNBR, diante da maior janela (em relação ao SBR) para a seleção da(s) empresa(s) e entrega dos produtos.
De outro lado, de concreto mesmo, temos apenas o contrato para um SNBR, o que pode não justificar o investimento.
Saudações.
Excelente matéria, parabéns . Eu só não entendo o motivo dos grandes meios de comunicação ( TV aberta ) não divulgarem esse tipo de informação com esse nível de qualidade. Tenho certeza que o grande público em geral iria se interessar e se orgulhar do trabalho e esforço de alguns pelo país. Não falo só de adquirir armamento de ponta , mas o que vem com tal empreendimento, desenvolvimento tecnológico, profissionais com alto nível técnico, etc. Não tenho dúvida que no futuro todos os envolvidos que tornaram possível essa conquista serão reverenciados pelo país. PARABÉNS.
VEIGA 104, há muitas razões para os grandes meios não de comunicação não divulgarem esse tipo de informação com esse nível de qualidade. Primeiro que não é interesse, não gera receita e eles não possuem repórteres com o mínimo de preparo para a área. Uma semana antes da nossa visita (para a imprensa especializada) eles fizeram a mesma visita para a grande mídia. O pessoal da Marinha falava de submarino e os repórteres queriam saber da intervenção militar no Rio. Essa é a grande imprensa que a gente tem. Imediatista e sensacionalista na sua grande maioria. Eles precisam fazer uma… Read more »
Na minha opinião, não vejo necessidade de se diluir todo o processo de nacionalização em várias empresas. Poderíamos fazer isso com a ICN, ou outra.
Mateus
Nem na iniciativa privada é adequado ter apenas um parceiro para fornecer partes do seu equipamento, eu entendo que a MB está corretíssima em distribuir o conhecimento. Isto garante que na falta de um, possamos contar com outro. Seja por problemas financeiros ou simplesmente carga do parceiro (ex. Nuclep e ICN que já estão sobrecarregadas).
O Brasil não perde uma oportunidade de perder uma oportunidade. Enquanto países travam verdadeiras batalhas intensas para espionar e obter tecnologia de outras nações (vide China, etc), nosso país simplesmente não consegue receber uma tecnologia importantíssima que está sendo oferecida de mão beijada no pacote. Êêêê Banânia!
Caro Augusto. O Alm. Othon fez várias operações de espionagem industrial para sustentar o programa nuclear. Acabou denunciado pelo MP.
Camargoer, não há a mais remota relação entre a atuação do almirante Othon como comandante do programa nuclear da MB e a denuncia por ele sofrida, que se deu por fatos ocorridos quando ele já era presidente da Nuclebrás. Essa denúncia está relacionada a esquemas envolvendo empreiteiras e o almirante teve ampla oportunidade de defesa assegurada pela lei. Eu sou um admirador incondicional do almirante Othon, e considero que essa ocorrência não diminui em nada o papel fundamental que ele desempenhou no programa nuclear da MB. Entretanto, não sou adepto de teorias da conspiração, que é do que se trata… Read more »
Augusto, eu não diria que foi de “mão beijada”. O preço foi bem salgado.
Poggio, todo mundo sabe que o Brasil está pagando (e caro) pelo PROSUB, até minha falecida avó. Quando eu disse “de mão beijada”, o contexto foi explicado acima: pouquíssimos países transferem tecnologias sensíveis a outras nações, que geralmente se utilizam de espionagem industrial e árduos meios de inteligência para obtê-las. O Brasil não precisou montar uma KGB, uma CIA para obter tecnologia sensíveis. Pagou caro e mesmo assim teve que contar com a boa vontade de outra nação (porque a França, assim como outros países fizeram, simplesmente podia ter negado o repasse dessas tecnologias) e mesmo assim não consegue reter… Read more »
Augusto, o preço que o Brasil está pagando para a França pelo Prosub é o mesmo que ela está gastando nos seis submarinos nucleares da classe Barracuda.
Pois é… pagamos caro e não conseguimos receber pelo que pagamos, apesar de o vendedor estar disposto a entregar… é de matar!
Caro Augusto, e o medo do Brasil em Fazer engenharia reversa e gerar descontentamento em outras nações!
A China por exemplo, não tem esse medo dai copiarem tudo de todos sem a mínima preocupação, aqui pagamos uma fortuna em tecnologias que podemos copiar via equipamentos que já operamos ou operávamos.
País de bananas é assim mesmo!
Com esses governos de quinta categoria que o Brasil tem, por mais que as Forças Armadas tentem nacionalizar, o resultado sempre fica aquém do planejado.
O país está acéfalo faz muito tempo, sem direção, nem estratégia.
A Bardella esta quebrada. Há anos. Como todo o setor de mecânica pesada. Não entendi porque foram bater na porta da Bardella. Precisa de um MEP. Não tem de quem comprar. As opções eram multinacionais ou o fornecedor dos franceses o que é muito natural. Precisa de baterias. A Eaton levou o fornecedor embora e a MB teve que procurar outro. Mas não era o que foi escolhido. Precisa dobrar chapas para fazer as calotas e os apêndices. Não tem prensa. Não entendi o que o país tem com isso. O setor de mecânica pesada quebrou lá nos anos 1970/80.… Read more »
Ter uma empresa no Brasil e contratar funcionários é algo para herói neste país. Com carga tributária que beira 40% e regras trabalhistas engessadas não é fácil ser empresário por aqui.
“O problema é a falta de um ambiente de negócios favorável no país, onde os ciclos econômicos não sejam tão agudos e não afetem profundamente as empresas.” . Se depender da solução desse problema, a nacionalização não dará certo nunca… Nossa economia ainda faz parte do capitalismo periférico, ultra dependente das commodities, portanto mais suscetível a sofrer com as crises do que as economias centrais. As crises cíclicas são parte indissociável do capitalismo, não tem como fugir delas. E isso vem de longa data. Não temos um mecanismo de poupança nos 7 anos de vacas gordas para depois queimar nos… Read more »
Ah, complementando: esse modelo de aquisição/utilização da super prensa me pareceu interessante. O equipamento caro ser adquirido pela Marinha e emprestado para operação pela empresa receptora da tecnologia, com os devidos cuidados contratuais. Assim, o investimento (e risco) da empresa fica menor, menos dependente da escala de produção, e a possibilidade de substituição da empresa que porventura quebre ou desinteresse é maior.
Que, salvo engano, é também o modelo da UFEM, que é propriedade da Marinha e está “emprestada” para operação pela ICN. Mais um indício de que o ProSub e sua continuidade têm mais possibilidade de sucesso.
Tudo bem?
Voces conhecem ou tem algum istorico mais detalhado sobre os projetos da Maritalia? Parecia interessante e uma volta as origens do submersivel, pois o conceito AIP deles era o de reservar oxigenio no casco para emprego da motorização diesel mesmo submerso.
o casco de alta pressão era formado por inumeros aneis (como roscas cilindricas) interligados. Tal como aqualung. Fizeram varios desenhos conceitos de pequenos subs em que apesar do tamanho, tinham excelente autonomia e velocidade para a categoria.
http://www.hisutton.com/images/It_GST-tubes.jpg
Diferente dos editores penso que em um programa desse tamanho aparecem fornecedores possíveis com, a “corda no pescoço”. Pegam o contrato e depois subempreitam. Comum, bastante comum em obras. É só dar uma olhada pelas rodovias e prefeituras pra ver a quantidade de obras não entregues, paralisadas, a maioria terceizadas e quarteirizadas. Quem contrata zela pelo contrato. Se a parte de lá roeu a corda, a responsabilidade é do contratante. Tem história pra contar das baterias, do MEP, das dobraduras. Tudo previsível pra quem tá ambientado com contratos. No final dará certo. Começa contrato e culpa a CLT. Começa projeto,… Read more »
Esteves Primeiramente não dá para fazer terceirização ou algo do gênero num caso como esse. Não é uma obra como outra qualquer. Não é a casa do seu Manoel da esquina que vai ser construída. As empresas que se comprometeram com o programa assinaram contratos com a Marinha. Profissionais dessas empresas (incluindo da Bardella) foram para a França aprender como se faz para depois voltarem e fazerem aqui. Muitos dos contratos foram assinados numa época muito diferente da atual. A própria Bardella não estava mal das pernas em 2010. Só que as coisas mudam e de forma muito radical no… Read more »
Essa crise foi um rude golpe ao PROSUB, espero ter um PROSUB 2 , para poder nacionalizar os TLP,mas vamos ter fé.
A grande mídia trabalha com a premissa de que o leitor brasileiro é um analfabeto funcional que só se interessa por futebol, escândalos e notícias sensacionalistas. Aí eles contratam jornalistas igualmente semi-analfabetos para gerar notícias do nível que amebas possam entender. E assim entramos num círculo vicioso, onde a grande imprensa é um fator de perpetuação da ignorância, ao invés de ser uma fonte de informações e reflexões para a evolução da sociedade. Por isso devemos ser imensamente agradecidos aos editores da trilogia, que geram conteúdo de qualidade internacional e contribuem para a concientização da sociedade sobre a importância dos… Read more »
Comparando a imprensa grande (nem sei se ainda existe) brasileira com os tabloides ingleses, as revistas alemãs e outros americanos, não vejo distância. Matérias militares, de defesa, que tratam de segmentos específicos não atraem público leitor. A quantidade de editoras e de livrarias também não significa que o país é ou está melhor porque Buenos Aires tem 25 livrarias para cada grupo de 100 mil habitantes X 3,5 de São Paulo e os argentinos estao numa tanga (com a) danada. O fato que despertou a grande imprensa no mundo foi o escândalo de Watergate. Editores e leitores voltaram os olhos… Read more »
“Alexandre Galante 11 de junho de 2018 at 14:06
Com esses governos de quinta categoria que o Brasil tem, por mais que as Forças Armadas tentem nacionalizar, o resultado sempre fica aquém do planejado.
O país está acéfalo faz muito tempo, sem direção, nem estratégia.”
Desde 1500.
Haveria um vídeo desta prensa produzindo uma calota?