Soldadores do PROSUB vão para a Europa trabalhar em submarino nuclear francês
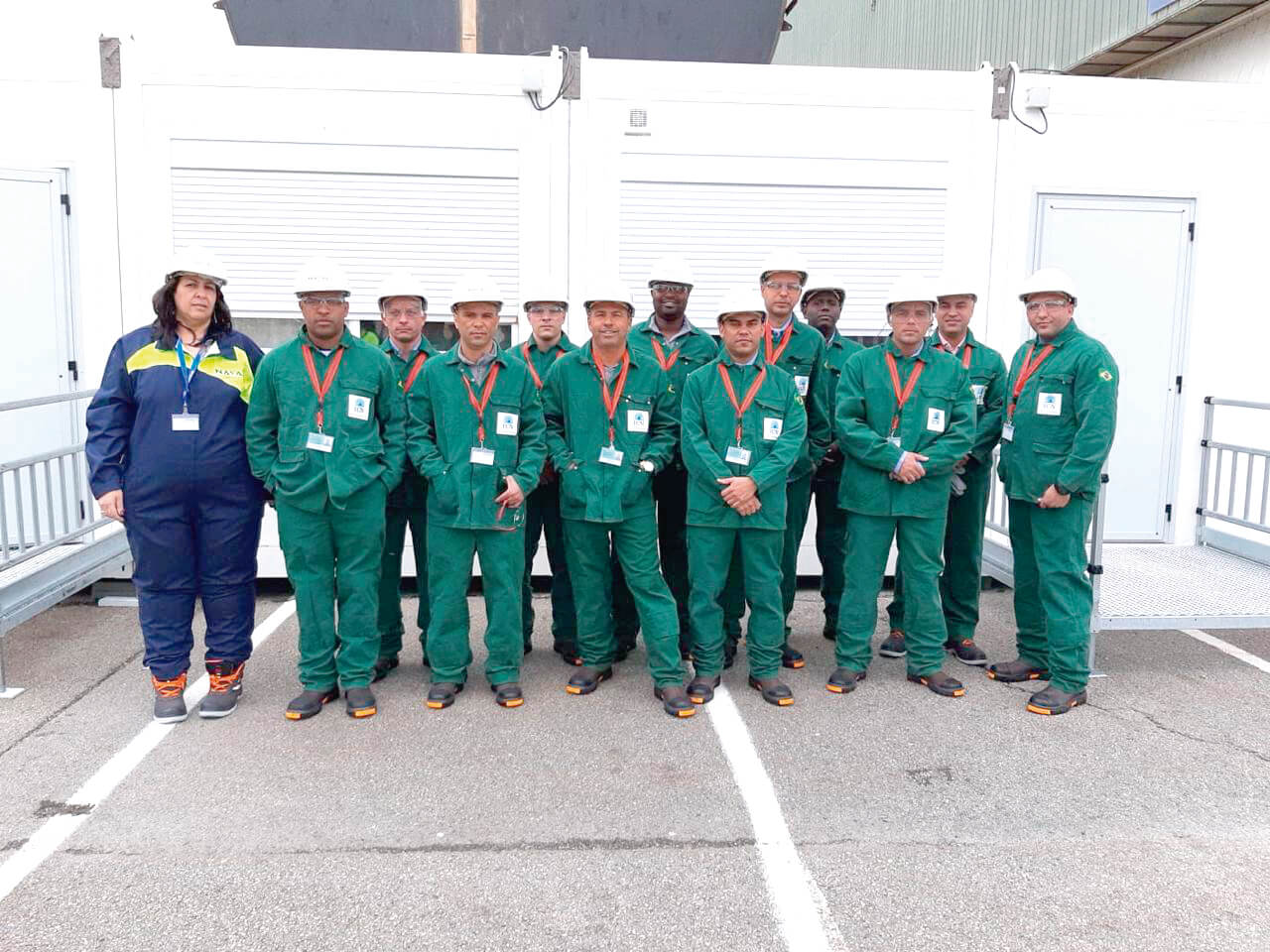
Integrantes são da escola de solda da empresa e curso faz parte do programa de transferência de tecnologia com a Naval Group
A Itaguaí Construções Navais (ICN) enviou à França treze integrantes para atuar na montagem do casco de um dos submarinos nucleares Barracuda, que farão parte da frota francesa. O grupo de soldadores brasileiros vai permanecer no país durante seis meses, em dois períodos de 90 dias. Eles foram formados na escola de solda criada pela ICN para o PROSUB (Programa de Desenvolvimento de Submarinos da Marinha), que, por meio da parceria entre os governos do Brasil e da França, tem a missão de fabricar 5 submarinos – 4 modelos convencionais (diesel-elétrico) e 1 movido à propulsão nuclear. O grupo de soldadores foi escolhido por ter alcançado um alto padrão de excelência no trabalho. Nunca nenhum deles s havia viajado para o exterior.
Na escola, localizada na sede da ICN, os soldadores passaram por uma formação completa, sendo qualificados em complexos processos. Antes de seguir para a França, fizeram testes rigorosos com o trabalho em chapas de 55 a 110 milímetros, que são as usadas nos submarinos nucleares e com as quais eles ainda não haviam trabalhado. “O resultado é impressionante, muitas etapas consideradas de alta complexidade técnica foram concluídas pelo grupo escolhido sem quaisquer erros, mostrando o quanto acertamos ao investir na formação desses profissionais aqui no Rio de Janeiro”, destaca engenheiro Luiz Antonio da Silva, coordenador de solda da ICN.
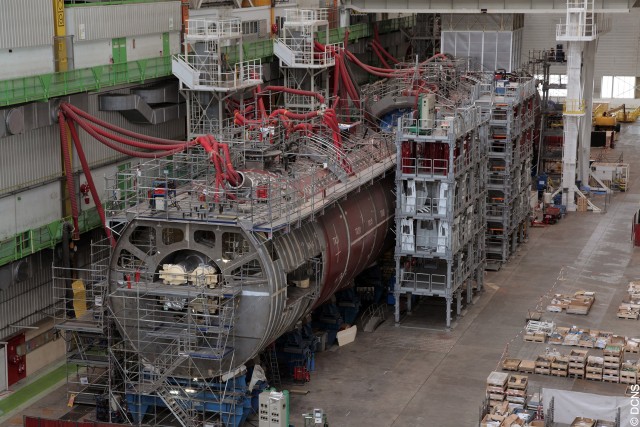
Escola de soldas
A escola de soldadores foi criada pela ICN em 2013 e já formou 174 trabalhadores. O treinamento dura, em média, três meses, e envolve a parte teórica e pratica. Atualmente, 129 seguem como integrantes da ICN.
Entre os que estão embarcando para França, oito são de Itaguaí e os demais dos bairros cariocas de Santa Cruz, Jesuítas, Campo Grande, além de Angra dos Reis. “Eles foram selecionados de acordo com os resultados apresentados e pela qualidade de suas soldas, índice de reparo e defeitos, além do comportamento, postura, assiduidade, comprometimento com o trabalho executado”, pondera o coordenador. O trabalho deles na França cumpre mais uma etapa do programa de transferência de tecnologia do PROSUB e também serve como estímulo ao desenvolvimento da população que reside ao redor do estaleiro, localizado em Itaguaí.
De acordo com Luiz Antonio, a ida do grupo para trabalhar no projeto nuclear francês representa o reconhecimento do trabalho desenvolvido na escola de solda da ICN em reproduzir o aprendizado adquirido junto à Naval Group no início do PROSUB.
“Este é um grande marco para a ICN e para o Brasil, mostrando que nossos profissionais estão altamente qualificados e preparados para grandes desafios, em especial, de construir o primeiro submarino nuclear brasileiro, sendo este um legado para a engenharia e a indústria naval do país”, finaliza.
Submarinos brasileiros
A fabricação de submarinos nucleares é tida como a mais complexa atividade construtiva em termos tecnológicos e capacitação de mão de obra. São necessários mais de oito milhões de homens hora de trabalho e a integração de quase um milhão de componentes, superando a fabricação de aviões de grande porte, caças militares e mísseis. O ponto alto do PROSUB é a transferência de tecnologia entre os países, assegurando que o país seja autônomo em seus futuros projetos de construção de submarinos.
FONTE: CDN Comunicação/Jornal Atual
Parabéns aos soldadores que vão a França….que sirvam de exemplo em suas comunidades, demonstrando que com trabalho árduo se pode conquistar cada vez mais.
Parabéns aos soldadores, e seus mestres que mostram que temos capacidade de aprender e entregar com excelência.
Que venham mais iniciativas e oportunidades.
Tenho certeza que esses soldadores devem estar muito orgulhosos, parabéns para eles e que sirvam de exemplo para outros.
Mas esse tipo de solda tem q ser executada com equipamento automático.
Caro Luiz, executar soldagens (não confundir com definição da solda) pode requerer ou um soldador propriamente dito (soldas manuais) ou operadores (soldas automáticas). Algumas soldagens do casco resistente do sub podem e devem ser executadas por meio de processos automáticos; um exemplo seriam as soldagens que usam processos denominados por GMAW (Gas metal arc welding), que no jargão de fabrica muitos denominam por soldagem MAG, e que utilizam gás ativo (por exemplo CO2) ou inerte (por exemplo Argônio) ou mesmo uma mistura (por exemplo, os corgons que são misturas de CO2 com Argonio) como meios para isolar o arco e… Read more »
Notar que na segunda foto da materia há vários dutos flexíveis insuflando ar em setores do Barracuda que está em fabricação, a maior parte dos quais está certamente fornecendo ar em locais onde se encontra um ou dois soldadores. Assim no momento da foto haveria algo em torno da ordem de uma duzia e meia de soldadores trabalhando concomitantemente. Veja que não seria possivel adiantar muito os prazos de fabricação pois não dá para querer botar cinquenta soldadores ao mesmo tempo dentro do casco…. Muita gente aqui no blog acha que os programas de fabricação de navios e aviões são… Read more »
Uma “Aula” de conhecimento. Obrigado, Rommelqe.
Meu amigo Cinturão de Orion (bom nickname esse…), muito obrigado.
Olá Rommelque,
Você saberia dizer qual o material de deposição (arame de solda) que se utiliza para o casco? Presumo que seja algo diferente do trivial que se usa.
Em sua opinião, os robôs de solda no Brasil ainda são caros? Já vi várias fábricas na China que adotaram robôs ocidentais. Se eles estão começando a usá-los mais extensivamente, acho que aqui também deveria haver esta oportunidade.
Prezado Smichtt: creio que o aço a ser empregado nas CCTs (agora redenominadas para FCTs) será muito provavelmente o S355 N/mm2 (o mesmo empregado nas MEKO 200HN gregas (ver na wiki: “The MEKO frigates have high-level specifications for shock resistance, stiffness requirements for the fire control and radar systems, and blast and gas pressure resistance to retain the integrity of the on-board weapon systems. The hull is constructed of high tensile steel with a yield strength of S355 N/mm² ‘structural steel grades”. )). Se considerarmos as seções molhadas do casco, a soldagem do skin plate (chapas em contato direto com… Read more »
Só complementado: usando GMAW (MAG) no costado do casco em aço S355 J2G3 (ou DIN St 52.3 N) o arame seria o ER-70S-6 sólido, com auto teor de silício; talvez seria conveniente usar só gas inerte ou seja passa de MAG para, MIG (pulsado).
Obrigado
https://www.youtube.com/watch?v=DqjgEzDav9Q . С 17 минуты , сварка взрывом , титана и стали . С 19 минуты , сварка титана в камере с аргоном . С 22 минуты электронно-лучевая сварка в вакууме .
Уважаемый Владимир, прежде всего большое спасибо за видео. Жаль, что я не знаю русский, но я знаю, что работал с четырьмя друзьями, которые учились у Патриса Лумумбы в Москве и окончили разные специальности (один инженер-гидротехник, другой инженер-механик, один специализируется на паровых турбинах, специалист по сварке!) и я с огромным уважением отношусь к высочайшему уровню технологий, которые вы практикуете. Ах, я забыл, я имел честь работать с шефом русской национальности, который учился здесь, в Бразилии, и стал бразильцем. Он тоже бежал из России … В любом случае, поздравляю. Российские технологии сварки очень важны, и для меня, я очень много работал с… Read more »
Para aqueles que eventualmente não saibam ler em russo: Caro Vladimir, antes de mais nada muito obrigado pelo vídeo. Pena que não sei russo, mas saiba que trabalhei com quatro amigos que estudaram na Patrice Lumumba, em Moscow, e se formaram em diversas especialidades (um é civil hidráulico, outro é mecânico de usinagem, um é especialista em turbinas a vapor, outro é especialista em…soldas!) e tenho enorme respeito pela tecnologia de mais alto nível que vocês praticam. Ah, ia me esquecendo, tive a honra de trabalhar com um chefe de nacionalidade russa que estudou aqui no Brasil e tornou-se brasileiro.… Read more »
https://www.youtube.com/watch?v=lqAmRIV7Z2M . С 24:30 Результаты гидродинамических испытаний в воде , сварных швов с помощью взрыва .
Exclente vídeo. realmente tão impressionante quanto o anterior. Parabéns.
Abraços
Спасибо . К сожалению я не владею иностранными языками . Через GOOGLE переводчик общаться нелегко . Если вам интересно можете посмотреть этот форум , на нём есть англоговорящие . http://forums.airbase.ru/2007/10/t58075–vms-stran-latinskoj-ameriki.html .
Muito obrigado Vladimir. Verei sim o seu link! Bom trabalho e felicidades!
Obrigado pela aula.
Parabéns a todos os envolvidos. Espero que com a expertise conquistada, estes nobres soldadores não sejam descartados futuramente, desperdiçando o conhecimento adquirido e exportação de subs em virtude de contenção de gastos.
E o salário?
Quando de fato ira começar a construçao do subnuc.
Pelo que temos visto no noticiário, o SubNuc está em fase de início de detalhamento do projeto executivo. Por ora, só há o projeto básico e uns 400 engenheiros capacitados para fazer o detalhamento, com ajuda dos franceses. Ou seja, saber quando começar a construção é coisa para cartomantes, só é possível um cronograma efetivo quando o projeto construtivo começar a tomar forma e for passando pelas fases de aprovação.
Estava vendo materias específicas que tratam dos prazos para execução de projeto executivo de um sub nuclear. São tipicamente algo em torno de mais de oito milhões de homens hora….só de dedicação direta, pois se formos considerar as horas dispendidas nos projetos de componentes (por exemplo, um MEP – motor elétrico principal, a partir do zero, vai consumir quase tanto quanto isso…), desenvolvimento hidrodinâmico de casco, propulsores, etc esse numero é muitas vezes superior. A quantidade de itens envolvidos (um item é por exemplo, um pressostato ou um motor) é superior a 1.000.000 (hum milhão de itens). E tem mutia… Read more »
Caro rommelqe, não se incomode com opiniões de torcidas organizadas. Esse é o lado negativo da internet, ter que ser tolerante com pessoas que combinam ignorância com arrogância. Mais acima você deu uma aula grátis sobre o processo de soldagem e ainda teve algum gaiato que teve a coragem de dar um negativo. Infelizmente a vida é assim, temos que conviver com gente invejosa e recalcada
Meu amigo JT8D, é isso aí, faz parte…Obrigado e grande abraço.
Parabéns a equipe selecionada, certamente são funcionários ímpares! Como empresário eu vejo a dificuldade que é encontrar bons funcionários, cada vez mais encontramos profissionais que de profissionais não tem nada, muitos deles não tem comprometimento algum com suas funções. Estes certamente foram escolhidos a dedo! Que baita oportunidade de vida e para carreira deles!
muito legal isso. parabéns aos profissionais que irão estar lá na França.
Rommelque É um privilegio contar com os abalizados comentários de quem entende e vive o assunto. Mas, lembrei de um caso clássico na história das soldagens. Na fabricação do tanque T-34, os russos observaram que os cordões de solda eram pontos fracos para a penetração de projéteis perfurantes. Como solução, os cientistas aperfeiçoaram o processo de solda de arco submerso. O arco submerso proporciona maior qualidade no cordão de solda. Todos sabemos que ao arco elétrico o aço perde carbono e a liga depositada difere do material do arame de aporte e da chapa básica. Colocar um fundente ativo que… Read more »
Caro Luiz Floriano Rosas, de fato ss soldas padrao “arco submerso” sao mesmo excelentes. Sua taxa de deposiçao é extraordinaria e o cordao resultante realmente e da mais alta qualidade. Usando novamente o exemplo das unidades geradoras de Itaipu, esse procedimento de soldagem foi largamente empregado e o exemplo mais incrivel sao os eixos. Cada unidade geradora possui tres eixos. O maior pesa em torno de 120 t e o menor apenas meras 15t ( se bem me lembro). Tais eixos em sua maioria foram forjados ( na fabrica da VIBASA em Taubate onde, alias, tambem foram forjados elementos para… Read more »